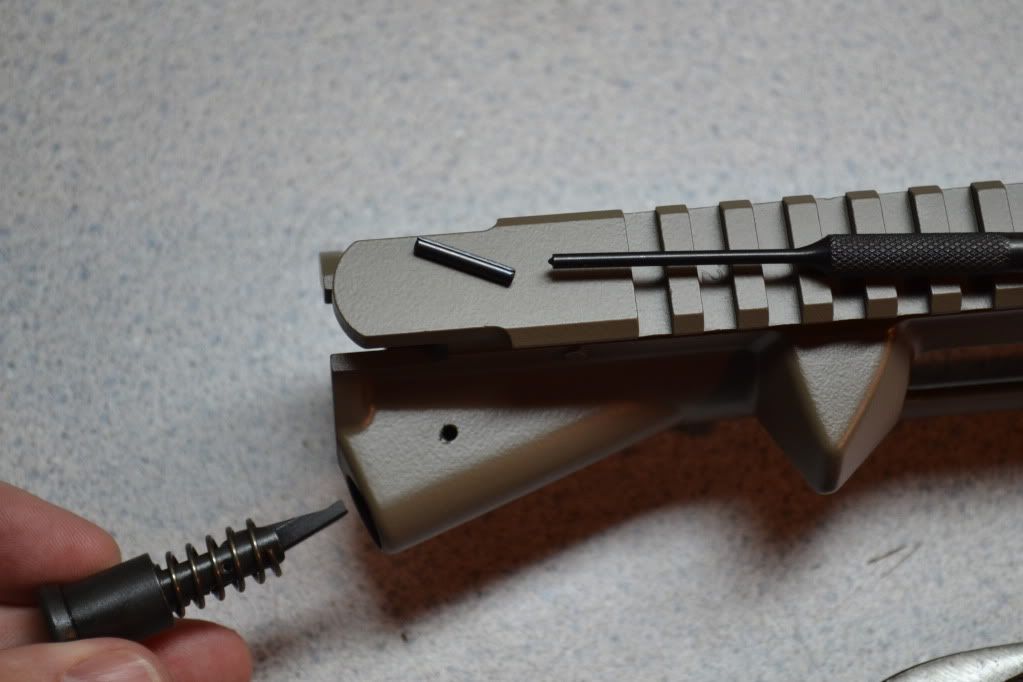
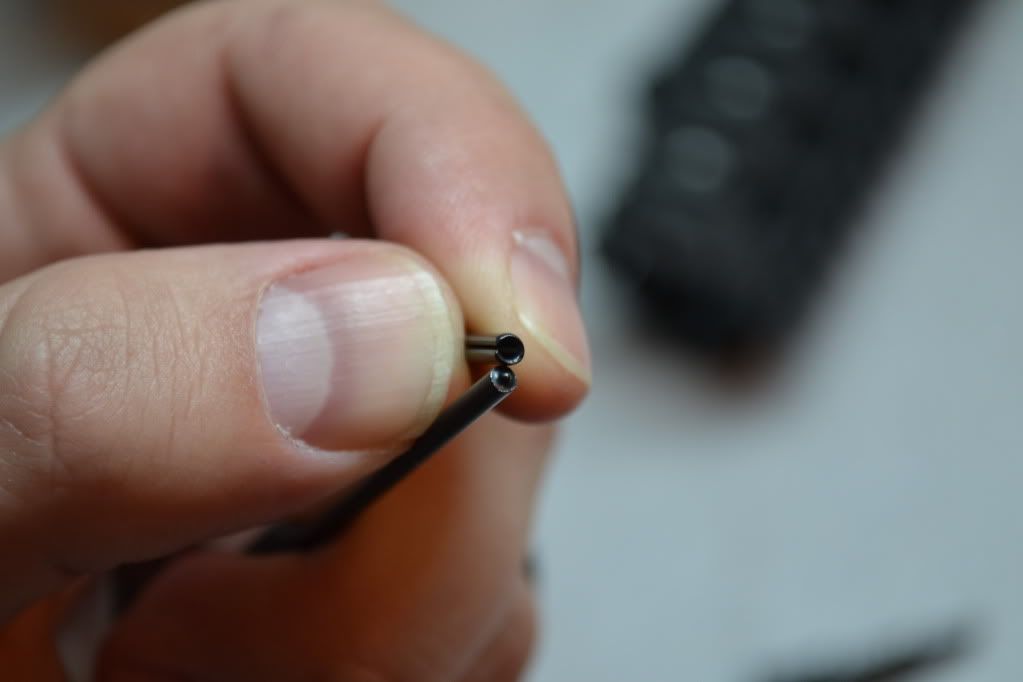
The forward assist goes into the big hole, and the roll pin goes into the conspicuously sized small hole there on the top. If you don't have three hands, get the roll pin started first before pushing the forward assist in (push it in as far as it will go before driving the roll pin all the way in). Some AR uppers don't have a forward assist, but they don't really add much more cost and you would be surprised at how useful it can be to quietly chamber check while in the woods and know that the bolt is seated. I bought the forward assist with spring and roll pin for like a whopping $16.
Next up is to install the ejection port cover. The ejection port cover pin has a small C-clip on it (one on the right) and you can see the notch where it goes (one on the left):
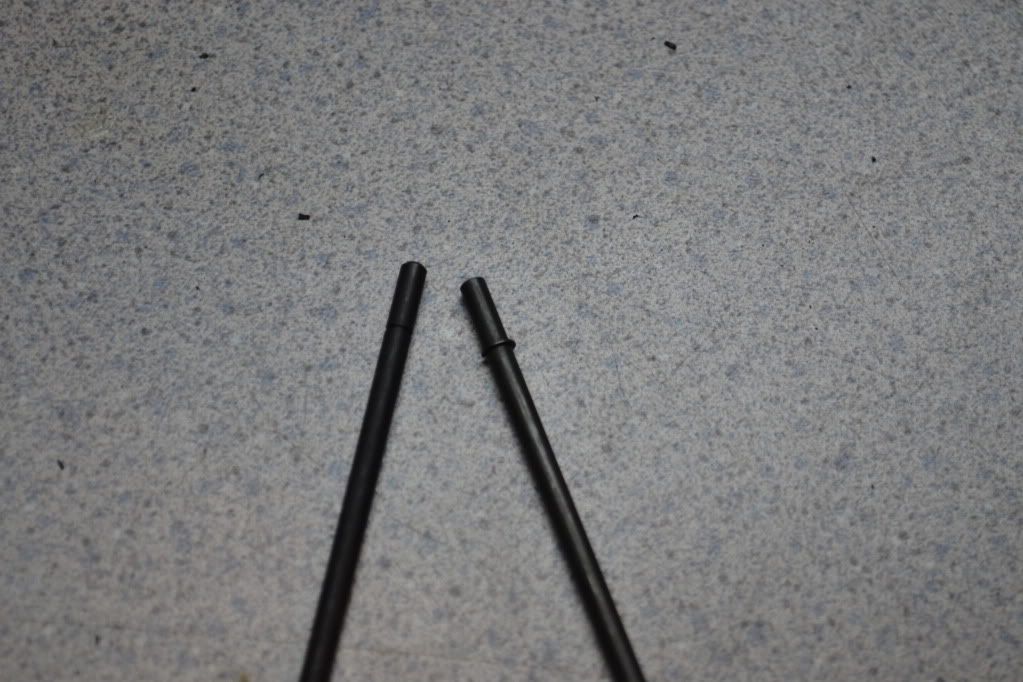
The C-clip side of the pin points towards the front of the receiver -- it just slides right in. As you're looking at it in the below picture, it goes in from the right to the left. The C-clip is on the right side of the pin. Start it through and then add the port cover, with the spring going in the gap. Putting the cover on takes about ten seconds total; you just have to be sure that the long tab on the spring goes against the door and the short tab goes against the receiver (looking at the spring in the picture, the long tab of the spring is on the left side and the short tab is on the right just below the ejection port):
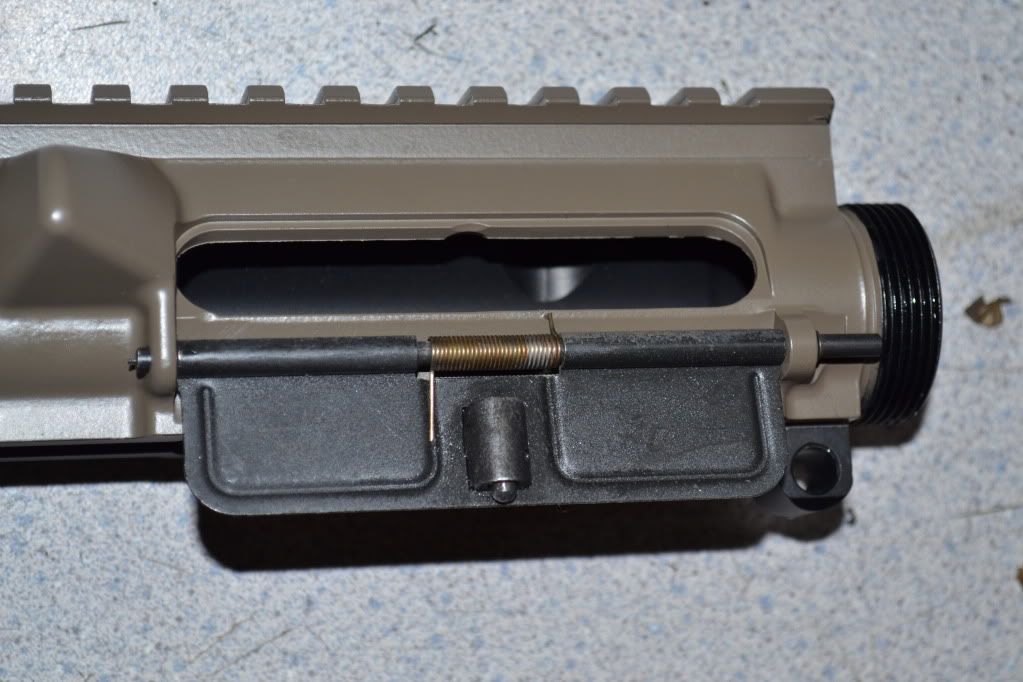
On to the gas block and gas tube. There's a single roll pin that holds them both together; take a moment to slide the gas tube into the gas block to see how it works; there's two holes on the end of the tube that correspond to two holes in the gas block -- small holes align for the roll pin, and the larger holes align to allow burned propellant to flow through them and operate the bolt. ***Notice the gas port on the gas tube is facing towards the bottom of the picture.*** When you assemble this beast, that gas port faces down towards the barrel:
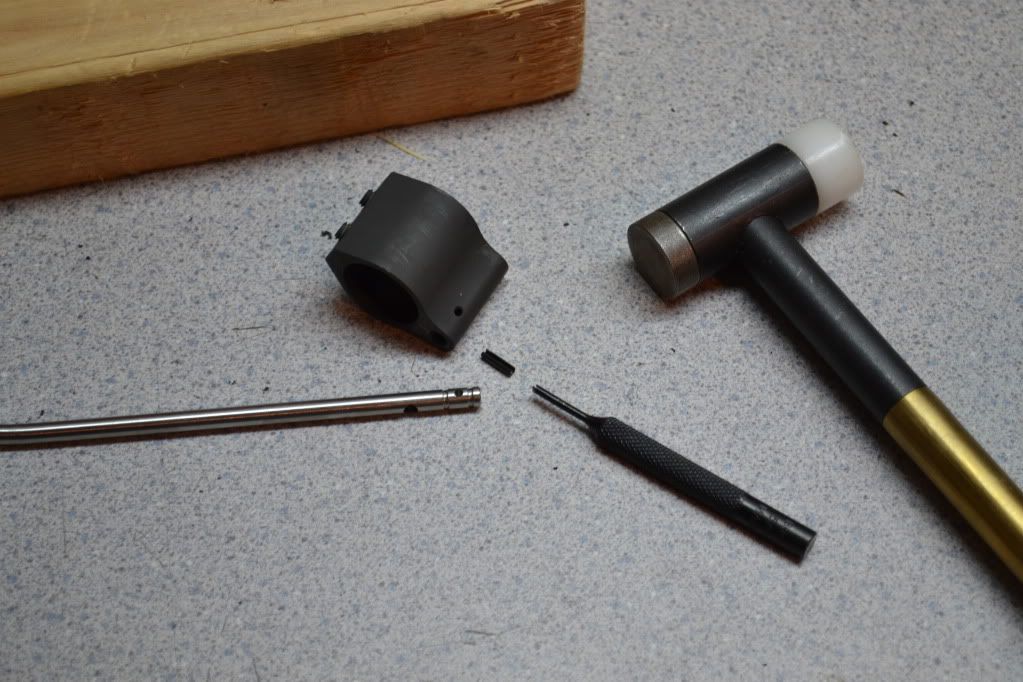
Before I install the gas tube with the roll pin, I measure the center of the big hole on the gas block and scribe a line to help me line up the gas block on the barrel (the side that faces away from the receiver, towards the muzzle). It just has to be a visible mark, and you can use a pencil or sharpie instead of a scribe:
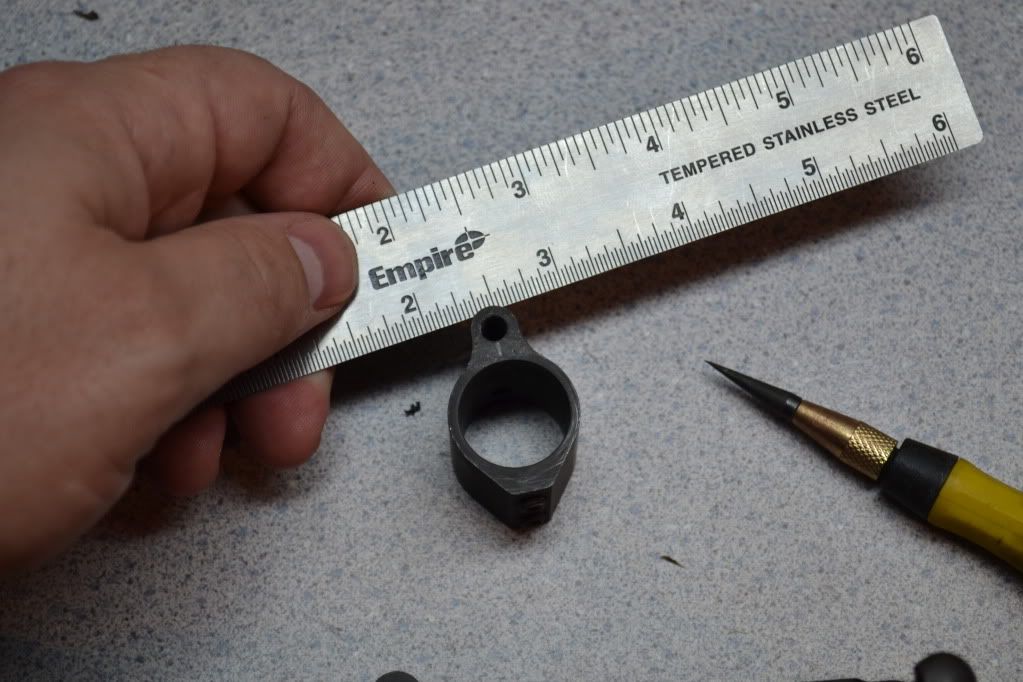

You'll see the reason to add that index line in a few minutes. Unless you have five hands, it's best to find a way to secure the gas block while you drive the roll pin through:
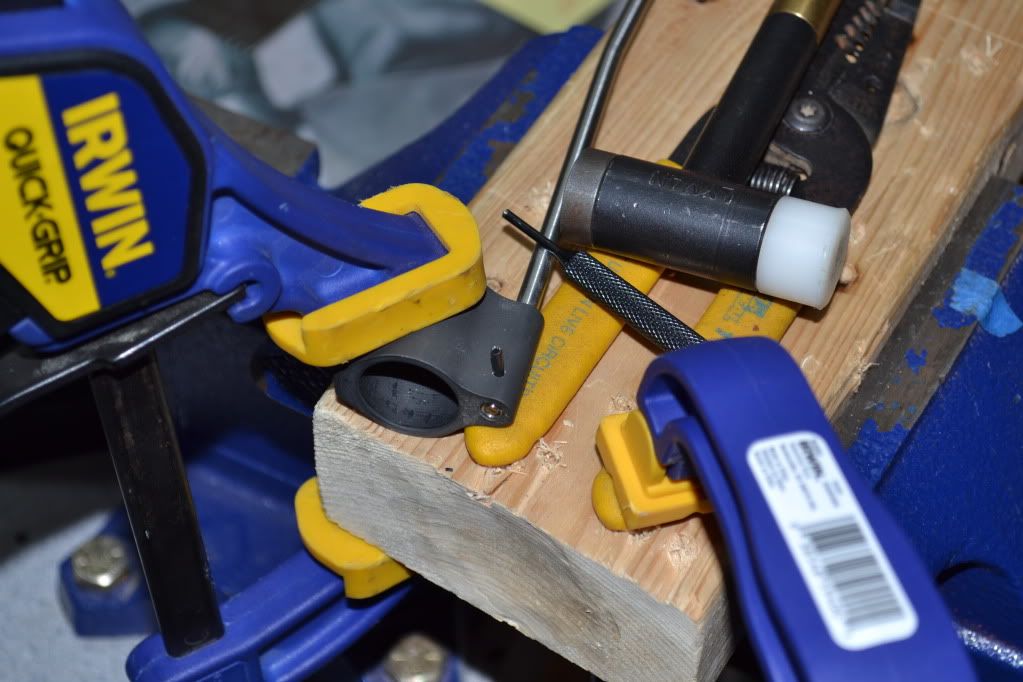
"WE HAVE WAYS OF MAKING YOU TALK!! MOOHOOWHAAHAHAHAHAH!!!"
This part can be a pain in the ass. Here's a pro-tip: while you have the gas block clamped down (be careful not to crush it!), push the gas tube in until the roll pin holes are aligned (be mindful of the ***gas port on the tube -- you want it facing the gas port on the inside of the gas block (as you can see it in this picture, it will be facing LEFT)) and then mark a line with a sharpie right where the tube enters the gas block. When you start tapping on the roll pin the tube will slide in and out, and it's a bitch to get things lined back up without an index.
On to the barrel installation. It's best to have a receiver block to secure the piece in a vice for assembly. I've gotten away without one before using two pieces of wood and a vice, but I don't reccomend it because if you're not careful you can crush your receiver. It's also not very stable. Either way, once you have your receiver settled in the vice, grease the threads (ONLY THE THREADS!! -- DO NOT get grease inside the receiver where the barrel extension goes!!)
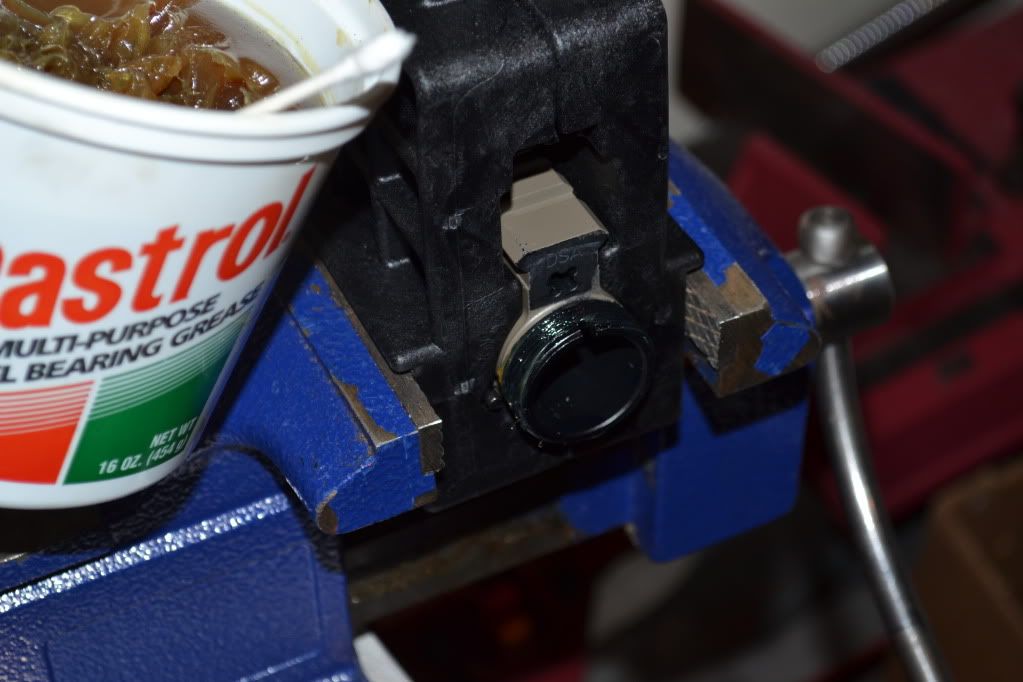
I have had good success so far using Castrol wheel bearing grease and applying it with a Q-Tip. The barrel extension fits into the big threaded hole in the receiver. Here's another pro-tip that I have independently verified that works great for maintaining accuracy when the barrel heats up: it's good to "bed" the barrel extension to the receiver. Benchresters use shim-stock, but you will probably have to order it; I use locktite, and it works fine and has improved my groups when the barrel warms up. Here's how it works:
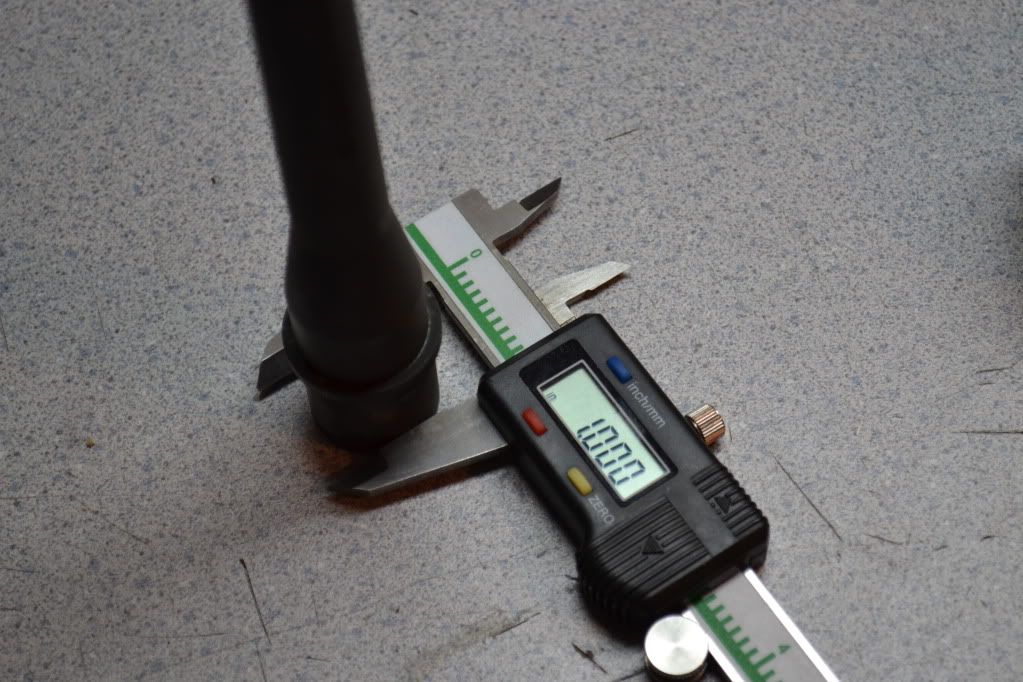
The outside diameter of the barrel extension on this barrel measures a clean 1.000", and the inside diameter of the hole where the extension is going to rest for the next 50+ years measures 1.002"
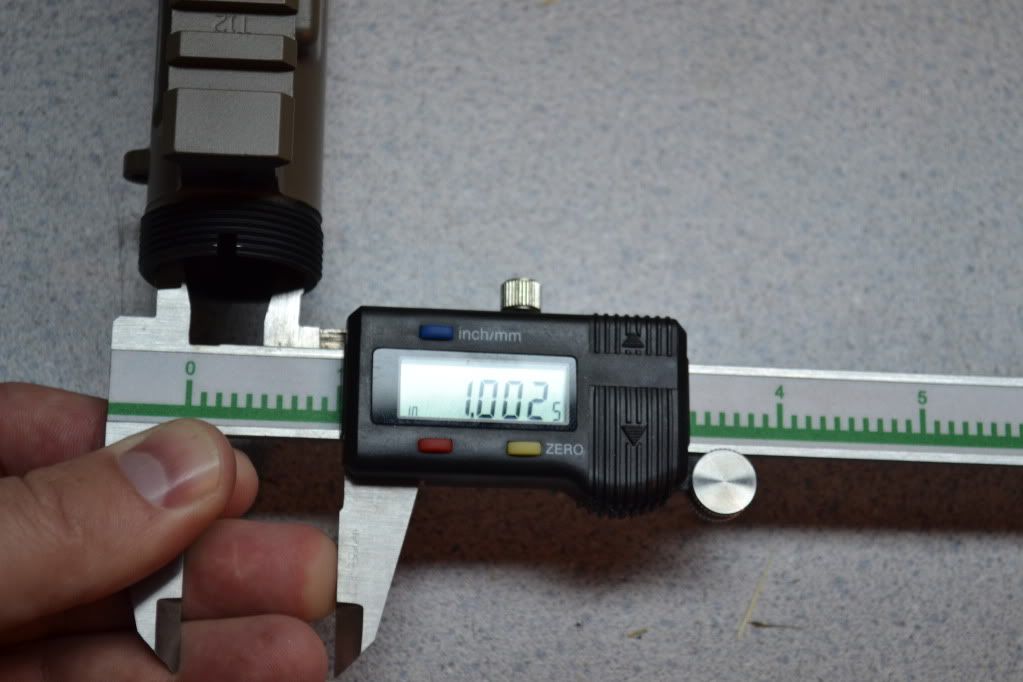
As far as AR receivers go, this DS Arms receiver is machined pretty tight. Some are not. The Les Baer receiver and barrel extention that's in my MK12, for example, was machined to tolerances my calipers couldn't even read to, so it didn't need to be bedded. When the steel in the barrel and extension heat up from firing, and when the aluminum in the receiver heats up, the metal expands, which can make your groups shift. By filling in the available space with Locktite or shim-stock, you're taking away that option. My group SIZES will still open up some when the barrel gets hot, but the point of impact does not shift.
With that said, I did bed this barrel extension, but you don't really have to if you don't want to. No biggie. To bed it with Locktite, you slather the outside of the extension and inside of the receiver where it contacts (I prefer blue Locktite for this), using your finger to get it even:

Now, WHILE THE LOCKTITE IS STILL WET, slide the barrel extension into the receiver, making sure to line up the indexing pin on the extension with the notch on the top of the receiver where the threads are. Hand tighten the barrel nut:
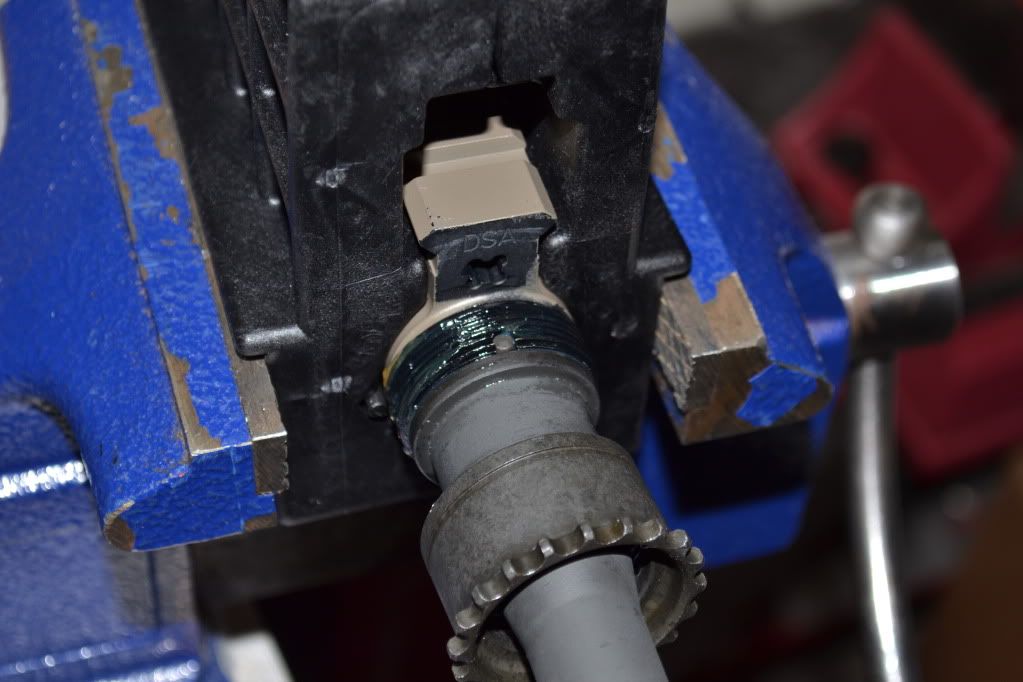
Tighten the barrel nut with an AR-15/M16/M4 barrel nut wrench; you want to do this three times to mate the threads together. So you crank it down (40 to 90 foot pounds if you have a torque wrench); loosen it up; crank it down; loosen it up; then crank it down tight again. I don't use a torque wrench because you have to line up one of the notches in the barrel nut to allow the gas tube to go into the receiver (you'll see in a minute), which means you may have to loosen the nut a bit to find a notch. I go by feel, keeping in mind that the receiver is made of aluminum and you can strip it or wring it off. I weigh just over 200 lbs, and I put about a 3rd of my weight into it WHILE SUPPORTING THE RECEIVER WHERE THE BARREL AND RECEIVER MEET with my left hand. I basically torque the end of the wrench downward with my right hand with most of my strength. The reason to support the barrel/receiver is so that you're not torquing it downward; the pressure from the wrench should only be going into the nut and the threads in a clockwise direction. If the end of the nut wrench is thin like a butter knife, or if you're a girl, you can hang a large wrench onto the end of it to give you more leverage:
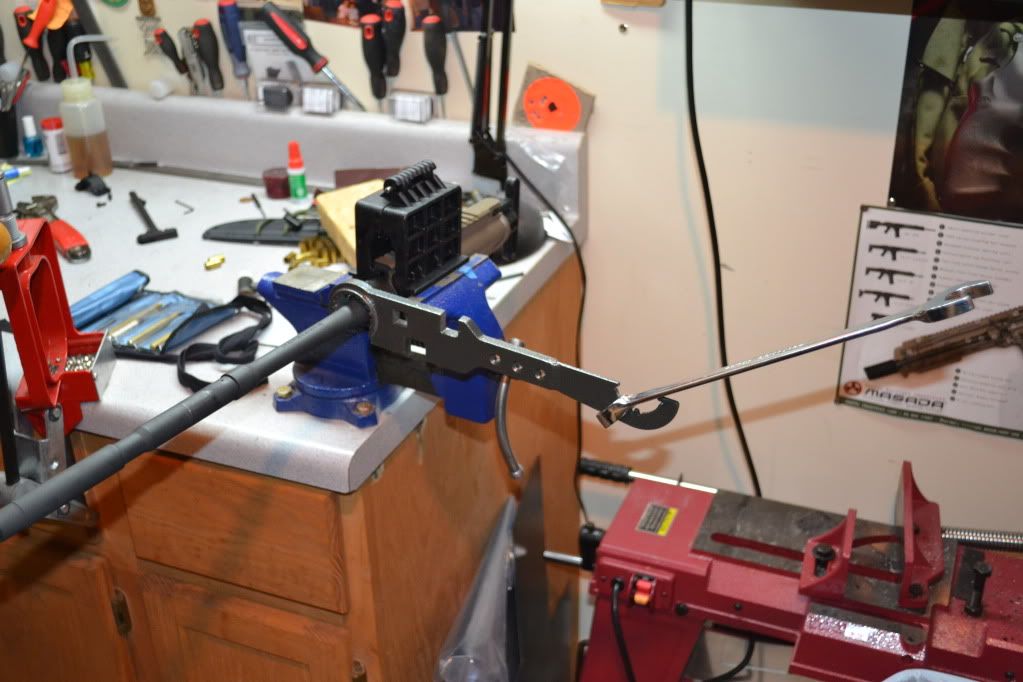
Once it's Gutentight, try the gas tube to see if it lines up okay. If it doesn't, then you loosen or tighten the barrel nut until the closest notch lines up. You want there to be a little side to side play at the hole where the gas tube goes into the receiver. That's important, because the bolt carrier key slides over the end of that gas tube inside the receiver, and if it doesn't have room to wiggle a bit the bolt carrier will chew it to pieces and your accuracy will suck:
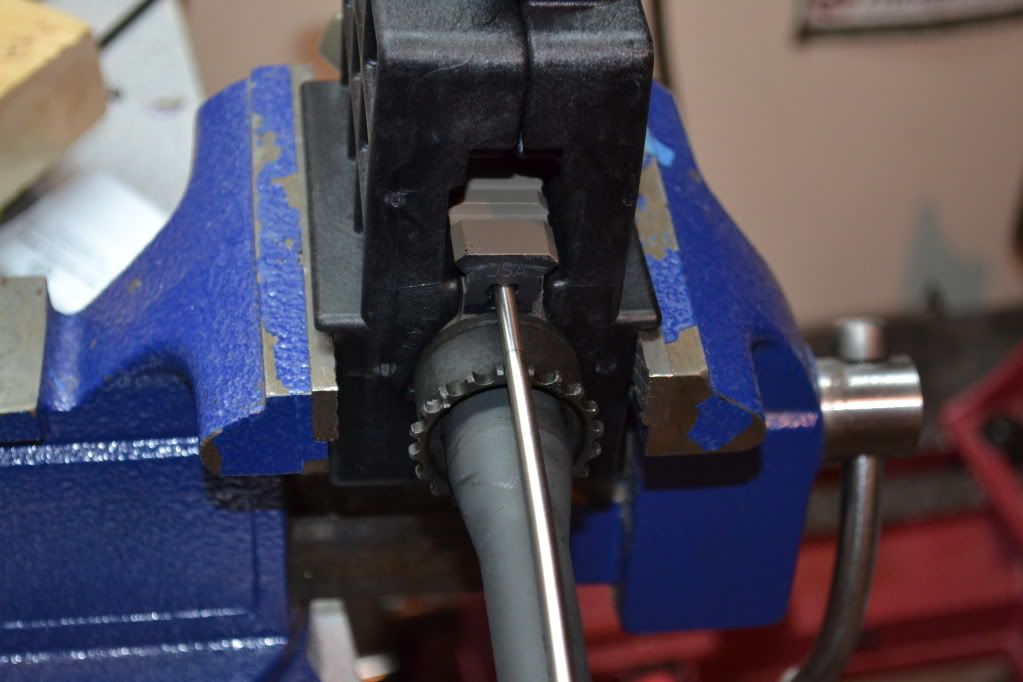
This is a good place to stop, take the receiver out of the vice, and clean out the still wet Locktite on the inside of the receiver where it squished out from under the barrel extension. Use a Q-Tip or something to that effect. If it has dried, try some rubbing alcohol or mineral spirits.
Now to install that gas block/gas tube assembly (hereinafter "assembly"). To make sure the gas port on the barrel is aligned with the gas port on the assembly, I scribe a line on the barrel to index with that handy dandy index line I scribed on the gas block. Don't scribe too deep (or use a pencil or sharpie):
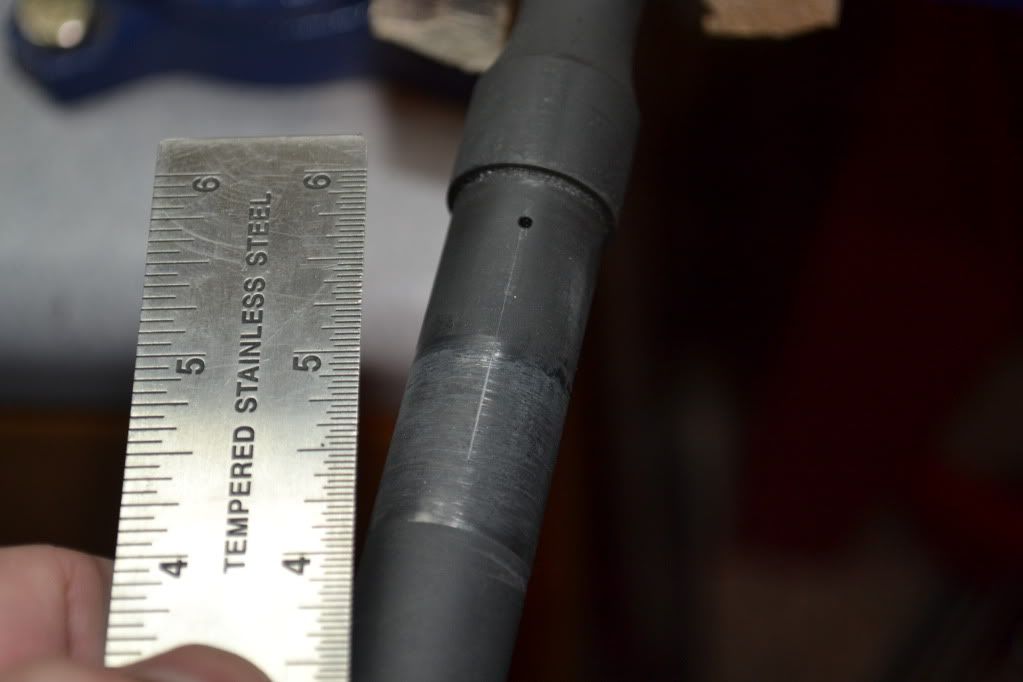
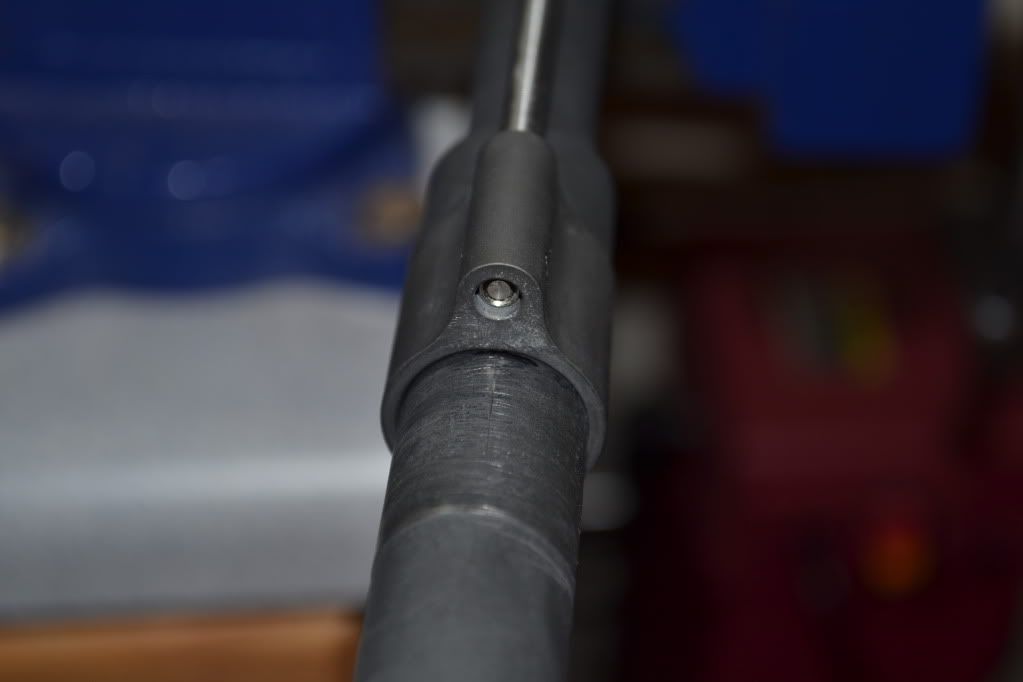
That last picture is not the best, but the two scribed lines line up. I've never had a problem lining them up this way. The gas tube now runs down the barrel and runs into the receiver like the picture three pics up. There's room for it to wiggle and everything is grand, so at this point I Locktite the two screws on the bottom of the gas block and tighten them to 20 inch pounds. Not all gas blocks are the same, so I skipped on the pictures on how it's secured. It's a Troy brand gas block and it has two hex screws that hold the thing on.
Moving on to the flash hider. There's all sorts of flash hiders, flash suppressors, muzzle breaks; I don't have much problem taming the fierce recoil of the mighty 5.56 NATO, but I'm also not planning on competing with it. I opted for the $20 standard issue A2 "birdcage" muzzle device thingy, and to install it you need a crush washer. The crush washer is shaped like a cup, and the concave part faces the muzzle threads and the A2 thingy screws down onto it:
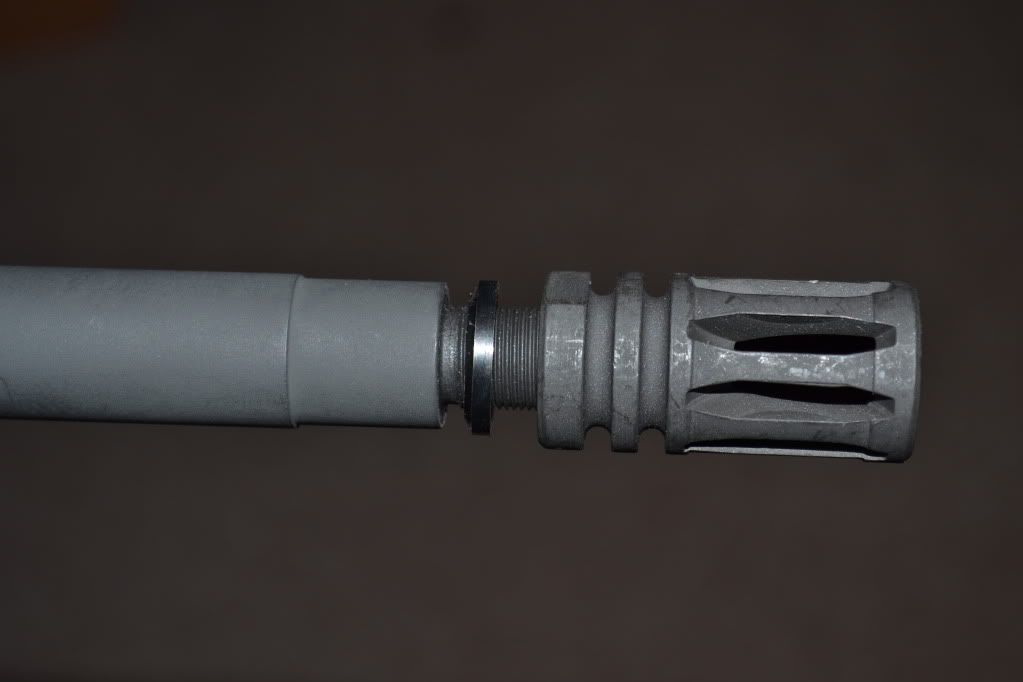
I'll admit that this part can be terrifying; a crush washer is called a crush washer because it crushes when you wash. . .er. . .tighten a barrel device against it. Isn't that clever? It takes quite a bit of effort to do it, which makes it feel like you're about to wring the end of the barrel off. It's purpose is to properly "time" the muzzle device; that is, to make the slots/ports at the end of the muzzle device point up, which leaves the closed portion of the muzzle device pointing down. On mine, once I screwed the A2 flash hider down hand tight, it needed a full 3/4 of a turn to properly time. I would crank it down hard, then loosen it a bit, then crank it down hard again. You can feel the washer crush as you do this (it feels like the threads are stripping, but they're not), and you'll notice the A2 will turn a bit more each time. Support the muzzle with your left hand while you tighten with your right so all of your effort is going into turning the muzzle device, and not bending your barrel. Stick a popsicle stick (or a small red-handled file) through the flash hider to give you an indicator of when it's level:
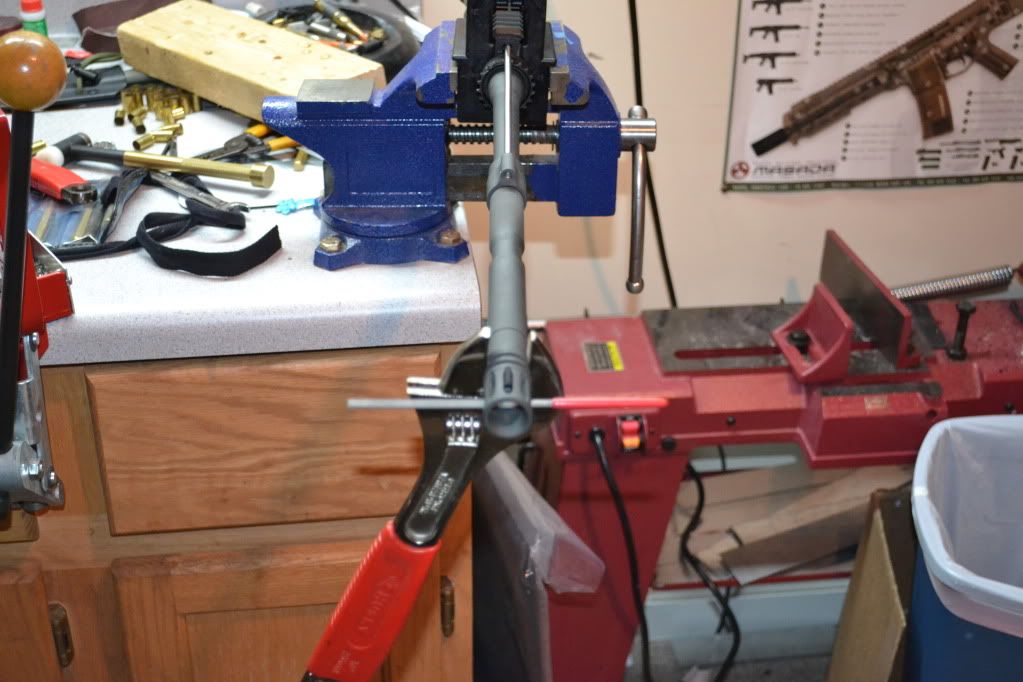
Good to go. Lastly, I installed the rail system and folding sights. The sights are a bo brainer, and for the Troy rail just follow the directions. It's a two piece design that free floats, and it mounts over a standard AR barrel nut with a clamp that uses five screws:
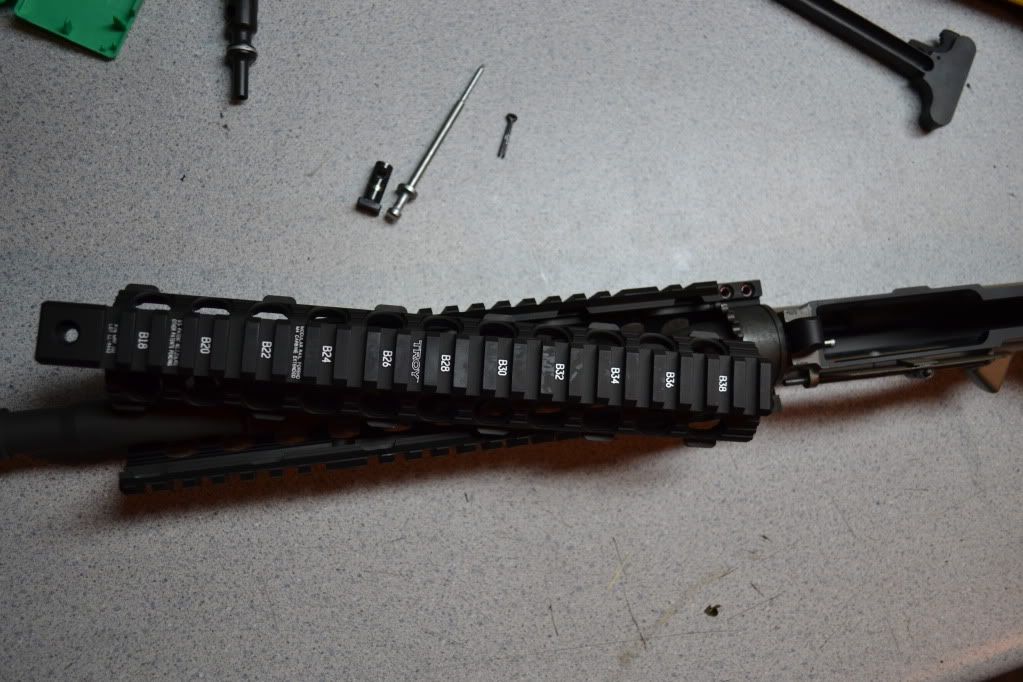
Looking at the above picture, the barrel nut sits down into the top half of the rail, and then the bottom half of the rail (it's facing the wrong way in the picture) snaps into the top half. You can see that the bottom half has little index tabs on both sides that fit into corresponding slots on the top half. Once they line up, the bottom half slides towards the receiver about 3/8", which locks the rail's tabs. There's a strap (it's in the instructions! Read the instructions!) that runs around the bottom of the barrel nut, connecting the two sections. I used the maximum recommended torque specs of 60 inch pounds, and it's solid. This rail has an anti-rotation design that fits against the receiver to keep it from turning. It's also not a gazillion dollars like a Knight's Armament rail. Here's a glamour shot of the finished product sans optic, which I will be ordering shortly. It's mounted on my DPMS lower for the
time being until I build the lower:
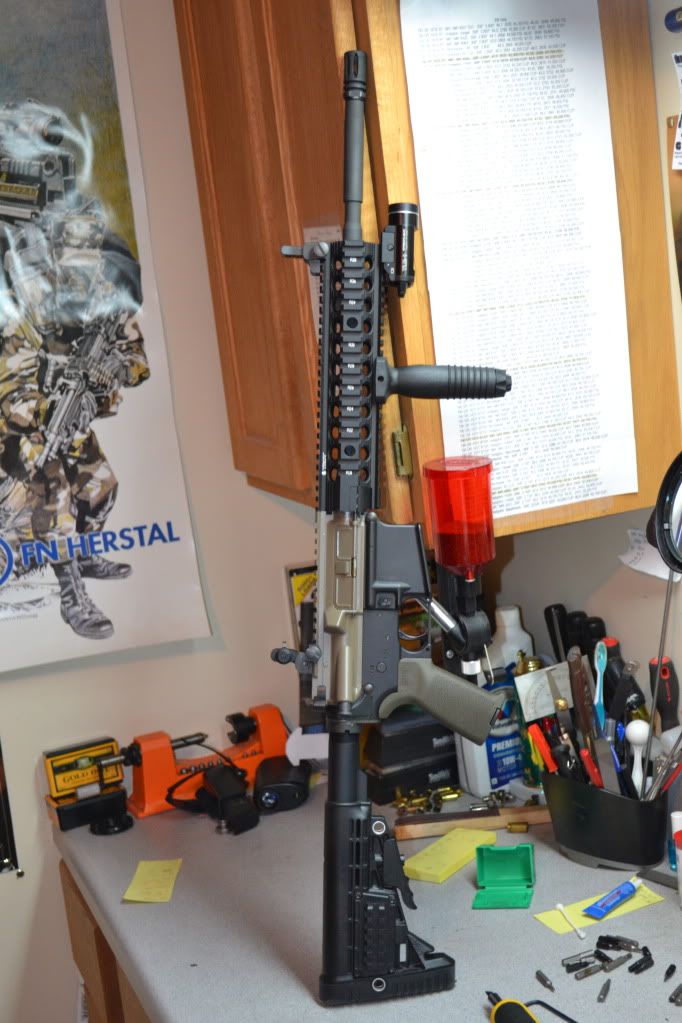
The rail is not as long as the rifle length rail on the little-AR-from-DPMS, but it will work great for its intended purpose:
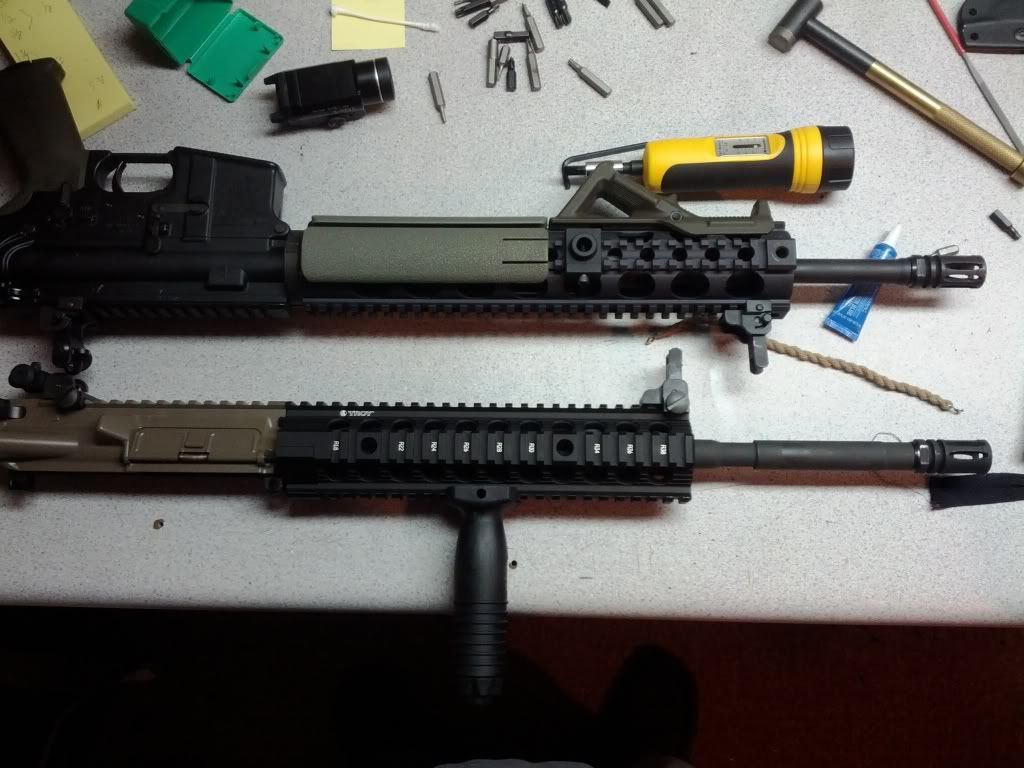
The advantage of using a longer rail on a carbine and putting your front sight way out there is that it gives you a longer sight radius, which translates into more precision available at range. There's also more rails for you to mount kitchen sinks to at that fighting-rifle class you're attending. All in all, putting an AR together is easy. It's also therepudic (if you don't have interuptions, then it's a clown-show). Give it a try sometime!
4 comments:
I've always been too afraid to try an upper build. did you go/no go gauge the barrel? do you have to headspace ARs like that, or are they more grab and go?
How do you align the gas block hole length-wise on the barrel? I understand the scribe lines for lining it up as the gas block revolves around the barrel, but what about moving it up and down the length of the barrel. How do you get that to line up?
Mike and Andy, the answer to both of your questions is basically the same. AR15/M16 barrels that you buy are actually an assembly; the barrel extension is a separate part, and it takes some machining on the chamber end of the barrel for the extension to "time" properly. The barrel extension has the lugs for the bolt to engage, and the actual chamber for the cartridge is in the barrel; in order for them to work in harmony, the chamber end of the barrel has to be machined down in a lathe until it will mate with the extension and headspace properly. If this isn't done correctly the head of the cartridge will not be supported and it can detonate when fired. Because of this, when you order the barrel it already has the extension mounted and headspaced for a standard bolt.
The extension is manufactured with an indexing pin installed in it that mates with a notch in the receiver. This pin serves two purposes: it ensures that when you slide the extension into your receiver, the feed ramps that are machined inside of the extension are plumb and facing the right direction; it also plumbs the gas port and faces it up -- the gas port is machined in when they assemble the barrel and extension, and it's alignment is already done for you. That single pin ensures that when you slide it into the notch in the reciever, everything is perfectly aligned.
To head off the next question, ordering a barrel sans extension would be a special order straight from whomever makes the actual barrel, and they will most certainly warn you that you need to get your own extension and ask if you know that you need a machine shop to install it. The barrels that you order online for your build have the extension on it already, so don't be concerned about whether the one F3 Tactical ordered for you has the extension installed -- it does.
There's a picture in this post that shows the barrel inserted into the receiver but the barrel nut is not screwed on yet; in there you can see the little round pin nesting in the receiver threads at 90 degrees. Let me know if this answers the mail for y'all, I know I can be long winded with this stuff!
Post a Comment